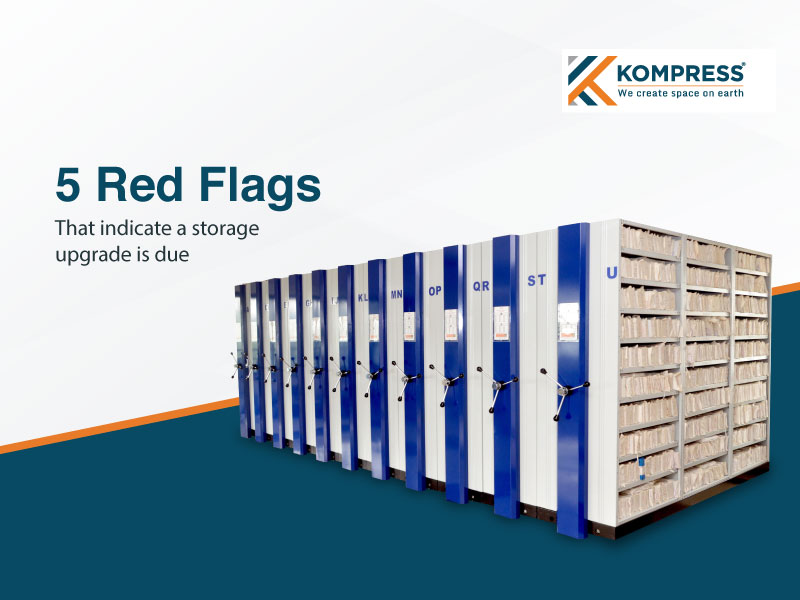
Is your Business in Need of a Storage Upgrade?
To answer this question, let’s begin by sparing a thought for the simple rubber band. You pull it – it stretches. You need it on a larger parcel, you pull it more – it stretches more. You push your luck further by stretching it even more, and perhaps it obliges again… But there comes a point when it will snap and cannot function as it should. You can still tie knots into it and push it to work, but its efficiency will be far diminished, keeping you on pins, wondering when it will collapse.
It is the same with storage systems. You keep piling inventory into it, it stands the pressure. You push and squeeze in those extra boxes and feel elated that you did it! You pile up, squeeze in, keep pushing to make space and fit yet another box, and feel you are magically managing. But the question is: How efficient is such a storage system? Does it feel like a wrestling match each time you have to put in or take out inventory? Is it worth the time, effort, and energy? What about the very important issues of safety and efficiency?
Don’t Wait for Breaking Point – Watch out for these 5 Signs Today
The wise old adage says: Prevention is better than cure… and it is very true for Inventory Management Systems. Inefficient storage facilities are bound to negatively impact operations and dent the bottom line. Why wait for that breaking point?
It makes good business sense, to be alert and look for the tell-tale red flags that should get your antennae up, and ensure an upgrade, before time runs out.
5 Signs that your Storage System Needs an Upgrade:
1. Space Wars
If your staff are complaining about space wars in your store room; or if filling an empty slot is like a game of musical chairs, it’s high time to look for an alternative. Your warehouse is definitely not a wrestling arena! Hence endlessly pushing in extra inventory, equates to sitting on a time bomb. You’ll agree that it doesn’t make sense to push your storage to the point of breakdown. Let’s not forget the rubber-band analogy. Consistently hitting full-house limits will hinder efficiency.
2. Changes in Storage Demands
Businesses today have to adapt to changing technologies, changing customer preferences, changing regulatory requirements, etc. Often these necessitate changes in storage needs and protocols too. Holding on to a system that did a good job in the past, cannot be the way forward in the face of changing demands. If your current system is increasingly feeling like a misfit, and requires constant compromises, it’s time to get an upgrade. The need of the hour is to have customised storage systems that meet your needs without wasting precious space, and simultaneously ensure a certain amount of flexibility.
3. Inability to Support Business Expansion
Every business wants to be on the prosperity path. With success come the out-growing of contemporary infrastructure including storage facilities. Has your business growth been fuelled by a substantially larger customer base; or new markets; or perhaps new merchandise; or increased production? Whatever the reason, while it’s time to rejoice, it is also time to review your storage facilities, because inventory management is an important function of every business worth its salt. Business expansion cannot go hand-in-hand with out-lived or out-grown storage systems, that do not unstintingly support business expansion.
4. Safety Issues
The goal of an efficient warehouse system is to have zero accidents, and zero errors. How efficient is your system? Remember, accidents and errors do cost money… and if accidents involve human lives or well-being, there’s a moral obligation too. Keep a close watch on your accident and error rates. An increase in these rates sure has an unpleasant story to tell. Whether the cause is damage, pilferage, negligence, or data compromise – all point to the need for a better system. It’s time to move to an efficient inventory system that is safe, secure, and systematic.
5. Operational Inefficiencies
Operational efficiency depends on a variety of factors that must work well together, with inventory management having a major role to play. Inefficient space utilisation, increased inaccuracies, slow processing time, increased order fulfilment errors, over-stocking, under-stocking, wastage, expired goods, inability to scale with growth, are some of the more obvious signs of operational inefficiencies linked to storage systems, and a crystal-clear indicator that your storage system needs an upgrade. Remember, operational inefficiencies are a drain on time, money and other resources, and silently eat into the company’s bottom line.
When you notice any of these five red flags, it’s a message that your storage facility needs an upgrade or perhaps a total revamp. Storage facilities play an important role in every organisation – large or small, and its importance in wholesale and retail businesses, factories, hospitals, malls, etc. cannot be underlined enough. Stopping with the red flags gets us nowhere, so let’s look for solutions too. Which leads us to the next question: What are the must-haves in the new or upgraded storage facility? Read further for the answers.
Essentials of an Optimal Warehouse Solution
- • Must Maximise and Optimise Space
Going vertical will save on ground space and maximise storage capacity per square foot. Ensuring the right types and sizes of storage units, will help optimise shelf space, because one size does not fit all when it comes to storage facilities. - • Should Strategize Layout and Storage
The physical layout and workstation design must help minimise unproductive pick-up travel time; and storage should be based on the industry, sales patterns, sales destinations, sales seasons, etc. - • Must Boost Efficiency via Technology
Technologically adept systems like Barcoding, Radio Frequency Identification Systems (RFID), Software for Warehouse Management Systems (WMS) etc. promote real-time inventory, automate error-free data collection, generate scientific analysis, and reduce documentation time, leading to better warehouse efficiency and productivity. - • Should Promote Smooth Accessibility
Accessibility is another important factor for improving warehouse productivity. An optimal warehouse solution makes use of Logistics and Software Support Systems, Material Handling Equipment, Automated Storage Systems, and Accessibility Enhancing Storage Systems like Selective Pallet Racking Systems, Drive-in/Drive-through Racking, Push-back Racking, Monorail Systems, Motorised Compactors, etc. - • Must Ensure Cost Efficiency
Look for storage systems that boost storage capacity without the need for expanding the warehouse. This brings in cost containment in terms of higher rentals or additional real estate costs. Also look for systems that reduce warehouse footprints, thus improving labour efficiency and saving on manpower costs.
Worried about Your Storage Red Flags?
Kompress is your one-stop shop for all warehousing and storage needs. Our storage systems are based on the science of space. What’s more is that our warehouse solutions are tailored to your specific needs and space constraints, and focus on significantly improving your warehouse efficiency and productivity. Kompress warehouse solutions are based on international concepts of storage and warehousing, curated by a highly experienced research team, bringing you world-class designs, and are meticulously manufactured at our state-of-the-art manufacturing facilities.
Visit us at www.kompressindia.com to view our wide range of safe, secure, sturdy, and simultaneously aesthetic storage systems, designed for every need, incorporating much more than the essentials of an optimal warehouse solution – because we believe in going that extra mile for customer satisfaction. With our immense experience, you can count on us to help you with value-for-money solutions, that make your warehouse more productive, and enables you to get more out of your valuable space.