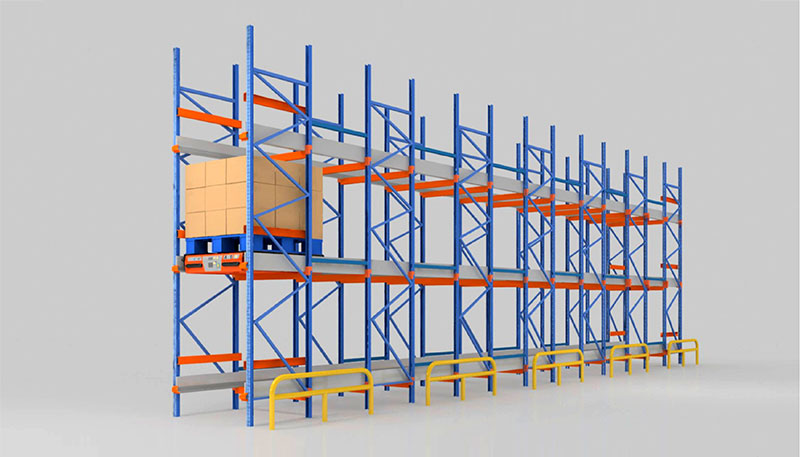
Everybody needs to store something! Whether you’re a solitary person with very few needs and living alone or whether it’s a small retail store or an institution or the world’s largest conglomerate… the need for storage is inescapable. In fact, the higher up the largeness pyramid you get, the greater the need for storage.
If not organised properly, storage can be a huge headache and an eyesore. For business and industry, the consequences go way beyond mere cosmetics and aesthetics – poorly organised storage can result in severe drainage of time and money as it can slow down operations and daily functioning.
Kompress has been in the business of providing innovative storage solutions for over three decades now. Launched at a time when storage solutions meant fitting together some angles and shelves and then cramming them with storage material, Kompress revolutionised the concept of storage with such solutions as automated storage and warehouse racking systems.
Automated storage systems are a big boon for any and every type of business. In fact, more than a boon, they have almost become a necessity. Today, when time and energy are also money, Kompress’ Automated Storage Systems help move huge storage facilities and provide access to even the most remote storage areas. Thus, they make storage and retrieval of diverse kinds of material and documents quick, easy and efficient, thereby freeing up staff time and energy for designated functions.
The following are some of Kompress’ innovative Automated Storage Systems:
Mini Load Automated Storage and Retrieval System
This system is designed to store small parts in a limited space and thus achieve extremely dense storage levels. A more economical storage option made from a, yet light-weight alloys, they are easy to instal, operate and maintain. They also maximise the available space by eliminating the need for aisles, which get created as required simply by effortlessly moving storage segments. Mini Load AS/RS Systems are ideal for compact storage and retrieval or where human involvement needs to be limited or completely eliminated.
Available in fully-automated or semi-automated options, they are flexible and efficient. Ergonomic and space-maximising thanks to multiple levels, their biggest latent benefit is that they help enhance productivity.
Pallet Shuttle Racking System
These are extremely versatile and flexible racking systems. They can be used in a wide range of temperatures – from freezer chambers that operate at -30oC to sultry warehouses where the temperatures may climb as high as 45oC. They are also suitable regardless of whether storage and retrieval process followsLast-In-First-Out or First-In-First-Out inventory formats.
In this system the pallet shuttles are remotely controlled, automatically carrying loads into the shuttle. Contemporary solutions, they represent a huge upgrade on conventional forklifts – even as they reduce accidental risk to person and property.
Designed to exacting European standards, Pallet Shuttle Racking Systems are available in multiple designs and configurations. They are cost-effective, help save operational time and are quick and sustainable.
High Density Motorised System
Kompress introduced India to the concept of ‘Zero Aisles’ or ‘Transferable Aisles’. Which work perfectly over limited area office spaces. But innovative as always, the company ‘transferred’ this concept to standard static warehouse racking too, thereby revolutionising the same.
By motorising entire rows of static racks, almost 50% of storage space is saved which, from a different perspective, amounts to nearly 100% increase in storage capacity. It enables warehouses to manage SKUs at the touch of a button, making storage and retrieval a breeze. Fitted with a slew of safety sensors, it is extremely secure.
With automatic, semi-automatic and manual operation options, it promotes enhanced energy efficiency. Its robust construction and compatibility with WMS software, make it well suited to modern, yet busy warehousing environments. It’s a great way to achieve high density storage by optimising available space.
Automated Guided Vehicle (AGV)
AGVs are a highly versatile system that can handle different types of loads including pallets, racks, trays, rolls and carts. What’s more, they are even compatible with various kinds of equipment including conveyors, stands and racks, in addition to floor pick-ups and drops.
AGVs are ideal for facilities where systemic changes are expected in the future, as they can easily be reconfigured to handle new or additional tasks. AGVs are a sensor-based system with embedded WMS. They are easy to instal, 24x7 reliable and efficient; reduce dependency on manual labour; are safe and minimise damage to product and property.