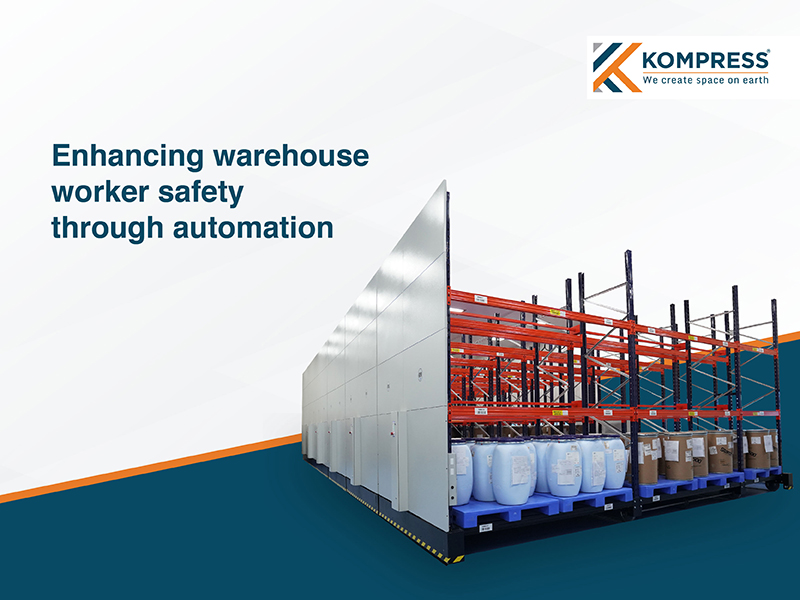
The need for automation
In the ever-evolving landscape of warehouse management, safety remains a paramount concern. As we push the boundaries of efficiency and productivity, we must never lose sight of the well-being of our most valuable asset – our workforce.
The modern warehouse is a complex ecosystem where humans and machines work in tandem, handling vast quantities of goods at unprecedented speeds. However, this high-paced environment also brings inherent risks – from physical strain and repetitive stress injuries to potential accidents involving heavy machinery. It's here that automation emerges not just as a tool for efficiency, but as a guardian of worker safety.
We at Kompress India Pvt Ltd, support and propagate automation mingled with innovation. The future of warehouse safety lies in the intelligent application of automation technologies.
Reduced manual handling
Automated systems have transformed the way warehouses handle goods, significantly reducing the need for manual labor and its associated risks. Conveyor belts, robotic arms, and automated guided vehicles (AGVs) now perform many of the lifting, carrying, and transporting tasks that were once done by human workers.
This shift has led to a dramatic decrease in the physical strain placed on employees, particularly when it comes to handling heavy or awkwardly-shaped items. As a result, the incidence of musculoskeletal injuries – such as back strains, sprains, and repetitive stress injuries – has notably declined in warehouses that have embraced automation.
Improved traffic management
The implementation of automated warehouse management systems has revolutionized the way goods and people move within a facility. These sophisticated systems use a combination of sensors, artificial intelligence, and real-time data processing to optimize traffic flow, significantly reducing the risk of collisions and accidents in high-traffic areas.
For example, automated systems can coordinate the movements of forklifts, AGVs, and human workers, ensuring that they follow predetermined safe routes and maintain appropriate distances from each other.
Some advanced systems even incorporate predictive algorithms that can anticipate potential congestion or collision risks and reroute traffic accordingly. This level of control and foresight not only enhances safety but also improves overall operational efficiency.
Enhanced inventory organization
Automated storage and retrieval systems (AS/RS) have transformed inventory management, bringing about significant improvements in both efficiency and safety. These systems utilise robotics and computer control to automatically place and retrieve loads from defined storage locations, eliminating the need for workers to climb ladders or operate forklifts at great heights. This automation drastically reduces the risk of falls, one of the most common and serious warehouse accidents.
Furthermore, AS/RS can optimize space utilization, often allowing for higher and denser storage configurations. This not only maximizes warehouse capacity but also ensures that items are stored more securely, minimizing the risk of falling objects. The precision of these systems also means that items are less likely to be misplaced or precariously positioned, further enhancing safety.
Reduced exposure to hazardous environments
Automation has been a game-changer in warehouses that deal with hazardous materials or extreme environmental conditions. In these challenging settings, robots and automated systems can now handle tasks that would be dangerous for human workers, significantly reducing the risk of exposure to harmful substances or conditions. For example, in cold storage facilities where temperatures can drop well below freezing, automated retrieval systems can operate efficiently without the need for human intervention, eliminating the risk of cold-related illnesses or injuries.
In warehouses handling toxic chemicals or radioactive materials, robotic systems can manage storage, retrieval, and even some processing tasks, minimizing human contact with these dangerous substances.
Similarly, in environments with poor air quality or the presence of airborne particulates, automated systems can operate without the respiratory risks faced by human workers. This shift not only improves safety but also allows for more efficient operations in these specialized environments, as automated systems can often work continuously without the need for protective gear or frequent breaks.
Improved ergonomics
The integration of automation in warehouses has led to significant improvements in workplace ergonomics, reducing the physical stress on workers and minimizing the risk of repetitive strain injuries.
Automated workstations can be designed with adjustable features that accommodate workers of different heights and physical capabilities. For example, height-adjustable picking stations can ensure that workers always operate at the optimal height, reducing strain on their backs and shoulders.
Collaborative robots, or cobots, can work alongside humans, handling the more strenuous or repetitive aspects of a task while the human worker focuses on elements requiring dexterity or decision-making.
Consistent performance
One of the key advantages of automated systems in warehouse safety is their ability to maintain consistent performance over extended periods. Unlike human workers, automated systems do not experience fatigue, distraction, or lapses in concentration, factors that often contribute to accidents in manual operations.
Robots and automated machinery can perform repetitive tasks with high precision and reliability, hour after hour, without any decline in performance. This consistency is particularly crucial in safety-critical operations, such as handling fragile or hazardous materials, where even a momentary lapse could have serious consequences.
Moreover, automated systems can operate 24/7 if needed, without the increased risk of accidents that often comes with night shifts or extended working hours for human employees. They also perform consistently in challenging environments, such as extreme temperatures or noisy conditions, which can affect human performance and decision-making. This unwavering performance not only enhances safety but also improves overall operational efficiency and quality control.
Inside the integrated safety ecosystem of automated warehouses
Automated warehouses are equipped with a multitude of integrated safety features that work in concert to create a comprehensive protective environment. At the core of these systems are advanced sensors and cameras that provide constant surveillance, detecting any anomalies or potential hazards in real-time. These are often coupled with sophisticated software that can predict and prevent accidents before they occur.
Physical safety measures include automated emergency shut-offs for machinery, safety light curtains that immediately halt operations if breached, and designated safe zones where human workers are protected from automated equipment.
Many systems incorporate redundant safety protocols, ensuring that if one system fails, others are in place to maintain a safe environment. Additionally, automated fire suppression systems, emergency evacuation guidance, and air quality monitoring are often integrated into the warehouse infrastructure.
Making the shift to automation
At Kompress India Pvt Ltd, we firmly believe that the future of warehouse operations lies in the harmonious integration of human expertise and cutting-edge automation.
It’s important to remember that automation is not a one-size-fits-all solution. Each warehouse has unique challenges and requirements, and the key to success lies in tailoring automated solutions to meet these specific needs.
As we look to the future, we see a world where warehouses are not just centers of logistics and distribution, but beacons of innovation in workplace safety. A world where accidents are rare, where physical strain is minimized, and where workers can focus on tasks that truly require human ingenuity and problem-solving skills.
The journey towards this safer, more efficient future starts with a single step – the decision to embrace automation.