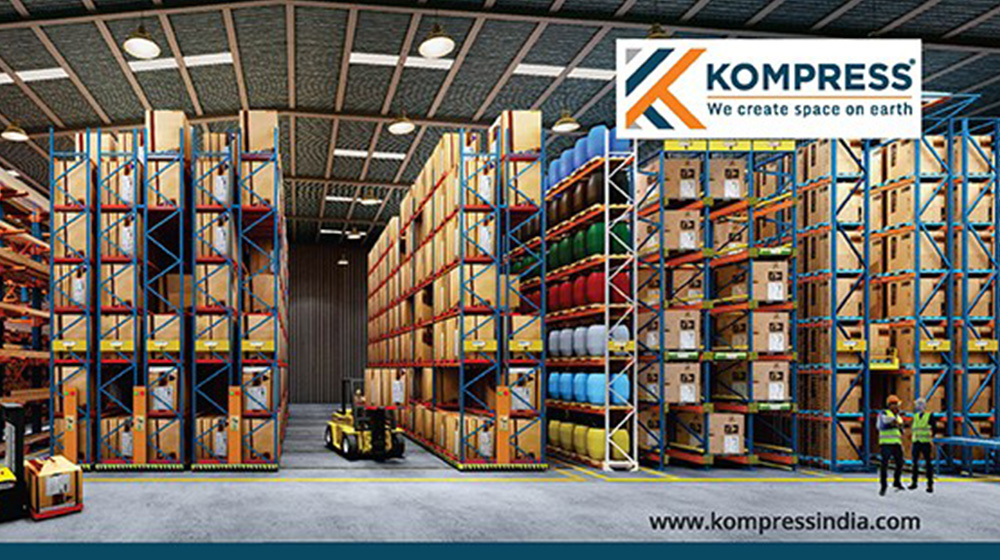
Time is Money…… Space is Money!Interested in seeing how time and space can make you money?A great place to start is your Warehouse!
Talking of Space - Every inch saved is money gained - more so with the phenomenal cost of real estate!
Talking of Time-Did you know that more than 70% of a picker’s time isoften spent on unproductive travel within the warehouse? Unfortunately every unproductive man-hour eats into your bottom line!
So let’s explore how time and space can be leveraged to improve warehouse efficiency and in turn make you money - via your improved bottom line!
Important Tips for Efficiently Managing Your Warehouse
1) Maximise and Optimise Space
- Go Vertical Instead of Horizontal
Every wasted square footisadditional money blocked in land or rentals and additional unproductive travel time. Hence vertical expansion through taller storage units must be your economically preferred choice. Double Decker Storage Compactors can almost double your storage capacity without expanding footprint.
- OptimiseShelf Space
Optimise shelf space by equipping your warehouse with the right types and sizes of storage units. Alsoensure that all items are stored compactly without compromising accessibility. Small items storedon large pallet racksunderutilisesspace,increases chances of misplacing things and makes retrieval difficult. Henceshelf allocation must be done keeping in mind maximum spaceutilisation.
2) Organise Storage as per Your Industry and Sales
A great way to improve warehouse productivity is to plan your physical layout and workstation design to minimise unproductive pick up travel time. It is therefore important to study your industry, your sales patterns, sales destinations, sales seasons etc. and plan your layout and storage based on this analysis.
Some pointers for organizing your warehouse to save pickers’ time are given below:
- Items frequently ordered/ shipped together can be kept together.
- Items with high sales turnover can be kept at the front of the warehouse.
- If your sales change seasonally, it may help to organize storage seasonally.
- If your industry has certain norms or statutory guidelines, then follow these.
A word of caution:
Revisit your analysis every few years to ensure your analysis is not outdated. Revisit your analysis every few years to ensure your analysis is not outdated.
Don’t trade off long term goals for short term benefits.
3) Adopt Enabling Technology
Technology is vital to improve warehouse productivity, thanks to its emphasis on speed, accuracy and efficiency. A warehouse with its complexity in terms of varieties, volumes, expiry dates etc. can overwhelm manual monitoring systems and lead to errors, wastage and loss.Using enabling technology can help you manage your warehouse with less effort and more accuracy thusimprovingefficiency.
Barcoding, Radio Frequency Identification Systems (RFID), Software for Warehouse Management Systems (WMS) etc. will help maintain your inventory real-time, automate error-free data collection, generate scientific analysis, reduce documentation time immensely and greatly simplify warehouse management -consequently improving efficiency and productivity.
4) Optimise Time ThroughLabourEfficiency
It is important toplan your warehouse activities sinceunproductive man-hours dent your bottom line.So let us look at some ways to optimise your warehouse man-hours and improve labour efficiency.
- Strategize your Pick-up Plans: Eliminate picking delays through logicalpickup plansthat will generate the shortest routes for picking and loading orders.
-Reduce Unproductive Travel Time: Your warehouse labour efficiency definitely improves when unproductive travel time is reduced through intelligent storage plans discussed earlier.
Provide Easy Access to Picking Bins: Reduce unproductive time by strategically placing picking bins so that they are easy to locate, convenient to access andsafe to manoeuvre.
- Improve Efficiency Through Training: Upgrade the skill and efficiency of your warehouse staff at all levels, through regular and relevant training,which will keep them abreast with innovationsthat improve warehouse efficiency.
5) Optimise Time Through Process Efficiency
Review your processes from time to time to incorporate innovations and improvements. Some tips in this direction are given below:
- MechaniseStacking and Picking Methods: Use efficient material handling equipment for compact storage and also for heavy items.Stacker trucks are a quick and efficient way to move pallets even in restricted spaces.
- Eliminate Non Value Adding Activities:Automate your processes wherever possible and weed out manual processes that do not add value.
- Ensure Aisle Space and Safety: Adopt methods that provide flexibility in aisle space. Transferable aisle storage system sare a good way to reduce aisle space without compromising on safety or convenience in aisle movement.
- Increase Packing and Shipping Area Efficiency: Ensure that all your packing material is easily accessible - whether it is shipping boxes, bubble wrap, tape, labels, tags or scissors. Time wasted searching for these, will reducewarehouse efficiency.
- Monitor and Eliminate Inventory Errors:Put systems in place to identify errors and their frequencies and put in place processes that will eliminate them.
6) Reduce Clutter – Increase Efficiency and Safety
Remember: Warehouse safety and efficiency are inversely proportionate to clutter.Neglecting these can be very expensive in terms of accidents, delays, errors, lost items, low morale etc. Neglecting these can be very expensive in terms of accidents, delays, errors, lost items, low morale etc.
To achieve a clutter free warehouse, neatly stack away goods in the right location soon after they arrive. Storage units, aisles, receiving stations, packing areas and workstations must be kept clutter free and free from thrash on an ongoing basis. Every shift must hand over a clean, clutter free warehouse to the next shift. This will contribute tremendously to efficiency and safety, and boost morale too.
7) Adopt Cyclical Inventory Verification
Increasing frequency of inventory verification will provide for better inventory control and reduce errors. It will also provide for timely identification of missing items and help put systems in place to avoid such errors and losses. Cyclical counts will reduce the verification load, as different areas will be verified at different times as per the defined monthly, quarterly or half yearly cycles.
8) Lean Inventory
Lean inventory translates into time, space and consequently money saved! The leaner your inventory the lesser your space requirement and lesser the time spent in stacking, documentation, inventory checking and control.
Pursuing the Japanese ‘Just in Time’ (JIT) principle to the extent possiblewill increase your bottom line, by saving your space and time.Analysis based stocking and reduction of safety stocks can contribute to the goal of lean inventory. Negotiating with suppliers to deliver with greater frequency will help you order and store smaller quantities and thus make your warehouse space more productive.
To summarise: Your warehouse can contribute to your organisation’s bottom line or it can be a white elephant which will eat into your profitability and resources. Henceorganising and managing your warehouseefficiently must be your priority. Using modern storage methods can certainly make your warehouse more productive. You have a host of modern mobile compactor storage systems to choose from -Mechanical Compactors, Motorised Compactors, Monorail Storage Systems, Double Decker Storage Systems, Manual Push Pull System Compactors and more!
If you are looking for ways to make your warehouse more productive and get more out of your valuable space, visit us at kompressindia.com and we’ll be happy to help.